Enterprise Resource Planning (ERP) systems have become essential tools for modern businesses, helping them to integrate various processes and functions into one unified system. By centralizing business operations, ERPs enable companies to increase efficiency, improve data accuracy, and foster better decision-making. However, the effectiveness of an ERP system depends on its core components, which address various aspects of business operations. In this article, we will explore the five fundamental components of ERP and how they contribute to the overall functioning of a business.
1. Financial Management
At the heart of every ERP system is financial management. This component handles the financial transactions and accounting tasks that form the backbone of an organization. It encompasses:
- General Ledger: The system tracks all financial transactions, providing real-time financial statements such as income statements and balance sheets.
- Accounts Payable and Receivable: Managing invoices, payments, and receipts, ensuring that cash flow is properly maintained.
- Asset Management: Monitoring company assets like equipment, machinery, and property to ensure their value is accurately reflected in financial records.
- Budgeting and Forecasting: Planning future financial performance based on historical data and current trends.
Why It’s Important: Financial management helps businesses track revenue, costs, and profitability. A robust ERP financial module ensures compliance with tax regulations, reduces accounting errors, and offers comprehensive insights into the financial health of the organization.
2. Human Resource Management (HRM)
HRM in ERP integrates all employee-related activities into one platform, streamlining processes from recruitment to retirement. It manages:
- Employee Records: Storing personal details, job roles, and salary information.
- Payroll Management: Automating the calculation of wages, tax deductions, and employee benefits.
- Talent Management: Tracking performance evaluations, promotions, and succession planning.
- Time and Attendance: Monitoring work hours, leave, and absenteeism.
Why It’s Important: By consolidating HR functions, businesses can reduce redundancy, minimize errors, and make better workforce management decisions. HRM also helps in compliance with labor laws and managing employee development efficiently.
3. Supply Chain Management (SCM)
A seamless supply chain is vital to a business’s success. The SCM component in ERP systems covers:
- Procurement: Managing vendor relationships, placing orders, and tracking deliveries.
- Inventory Management: Monitoring stock levels, ensuring optimal stock availability, and reducing wastage.
- Warehouse Management: Organizing storage, handling, and dispatching of goods.
- Logistics: Coordinating the transportation of goods, both incoming and outgoing.
Why It’s Important: SCM helps in optimizing the production process, reducing delays, and improving customer satisfaction. With a unified view of inventory and procurement, businesses can anticipate needs, reduce costs, and maintain efficient supply chain operations.
4. Customer Relationship Management (CRM)
The CRM component of ERP manages the entire customer lifecycle—from lead generation to after-sales service. It includes:
- Sales Management: Handling the sales pipeline, customer orders, and contracts.
- Marketing Automation: Managing campaigns, lead nurturing, and customer engagement strategies.
- Customer Support: Tracking customer issues, complaints, and inquiries, ensuring timely resolutions.
- Sales Forecasting: Analyzing historical sales data to predict future sales trends.
Why It’s Important: CRM is essential for building long-lasting relationships with customers. A well-integrated CRM module helps businesses manage customer data, improve service, and drive growth through better sales and marketing strategies.
5. Manufacturing and Production Management
For businesses involved in production, the manufacturing module in ERP is critical. It covers:
- Production Planning: Scheduling and managing production orders, aligning them with demand forecasts.
- Bill of Materials (BOM): Tracking raw materials, components, and assemblies required for production.
- Shop Floor Control: Monitoring the progress of manufacturing tasks, machine availability, and workforce efficiency.
- Quality Control: Ensuring that products meet specific standards and managing any defects or deviations in the production process.
Why It’s Important: This component allows businesses to streamline production operations, improve efficiency, and reduce wastage. By ensuring that manufacturing processes are aligned with demand, businesses can optimize production schedules, reduce costs, and deliver products on time.
Conclusion
ERP systems are designed to bring together critical business processes into one unified platform. The five core components—Financial Management, Human Resource Management, Supply Chain Management, Customer Relationship Management, and Manufacturing and Production Management—form the foundation of a robust ERP system. Together, they enhance efficiency, promote transparency, and empower businesses to make informed decisions. Implementing an ERP system with these components can lead to streamlined operations, increased productivity, and sustainable growth.
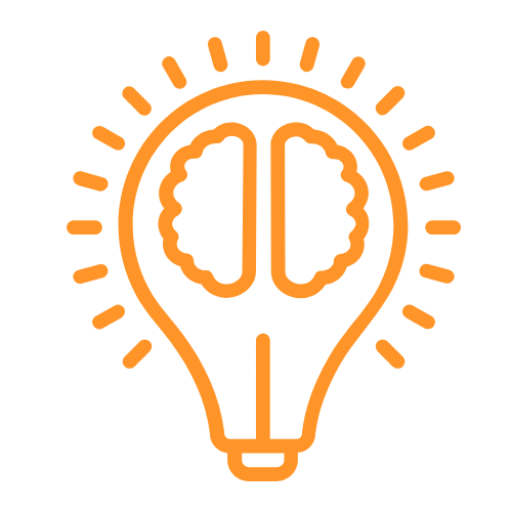
At IntelligentMind, we deliver AI-powered solutions that optimize operations, boost productivity, and drive growth. Unlock the potential of AI for your business success.